The Interplay of Product Design and Manufacturing Excellence
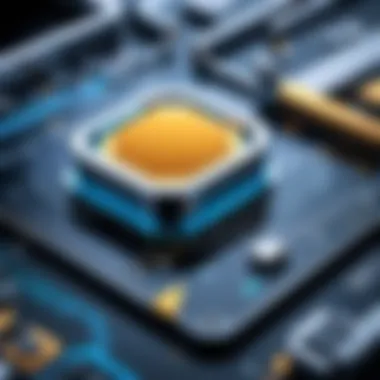
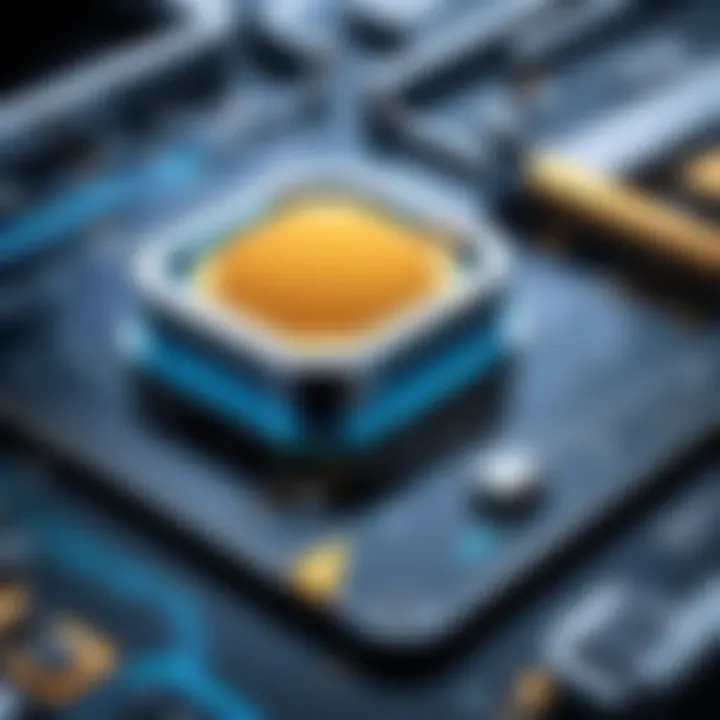
Intro
The interplay between product design and manufacturing stands out as a key factor that can determine the success of a product in today's competitive environment. As industries evolve, both seasoned professionals and new entrants in manufacturing must appreciate how design principles significantly impact production processes.
From material selection to efficient design practices, understanding this relationship is paramount. Key concepts include the importance of integrating design early in the manufacturing process and iterative feedback which ensures that both design and utility align with consumer needs.
Additionally, it is crucial to explore the challenges encountered when balancing design aesthetics with manufacturability, as neglecting one often leads to increased costs or decreased functional appeal. As technology advances, new tools emerge that streamline the connection between design and manufacturing.
In the sections that follow, we will dive deeper into each of these aspects, highlighting case studies that illustrate effective product design strategies and exploring future trends that hold potential for revolutionizing manufacturing practices.
The Connection Between Design and Manufacturing
Effective product design is not just about visual appeal. It encompasses functionality, usability, durability, and manufacturability. Each decision made during the design phase directly impacts how easily a product can be produced, its market introduction speed, and overall cost. Understanding this type of interconnectedness allows manufacturers and designers alike to create products that not only sell well but also maintain efficiency and profitability during production.
Design Principles Influencing Manufacturing
- Design For Manufacturability: Designing products with manufacturing capabilities in mind can reduce production stress and shorten timelines.
- Material Selection: Choosing appropriate materials ensures durability while still being cost-effective during production.
- Iterative Design Processes: A feedback-driven approach allows for refining the design continuously, leading to better end-products.
"Design is not just what it looks like and feels like. Design is how it works." — Steve Jobs
The effective integration of these principles can pave the path to seamless manufacturing relations, thus fostering innovation and ensuring consumer satisfaction.
Case Studies: Successful Design Strategies
Examining real-world cases helps to elucidate how design and manufacturing intersections have led to successful outcomes.
For instance, Apple Inc. streamlined its manufacturing lines by extensively testing the assumptions made during product design. This approach not only enhanced efficiency in production but also ensured the final product met high standards of usability and quality without excessive costs.
Similarly, Tesla has vitalized the automotive industry through aggressive yet effective design principles that allow for efficient production lines while also accommodating evolving consumer needs toward sustainable vehicles.
These instances emphasize the importance of designing for manufacturability, underscoring the value of adjusting designs to meet manufacturing capabilities rather than merely adapting manufacturing processes to fit designs.
Future Trends in Design and Manufacturing
Looking ahead, various trends will likely continue to redefine how product design interacts with manufacturing. These may include:
- Increased Automation: The use of artificial intelligence and robotics will streamline production stages, enhancing precision and reducing waste.
- Sustainable Design Practices: As consumer demand shifts, designs incorporating biodegradable materials and sustainable alternatives will garner attention.
- 3D Printing Advancements: The integration of additive manufacturing offers unprecedented customization and flexibility in design.
As manufacturers and designers embrace these trends, they will greatly influence overall productivity, customer satisfaction, and ultimately sales. Looking ahead, particularly in a tech-driven landscape, one can appreciate the reservoir of potential waiting to be tapped.
Finale
In summarizing the essential connections made throughout this article, it becomes evident that effective product design goes beyond socalled creativity. It involves strategic decisions that resonate strongly with manufacturing processes, ultimately shaping how successfully a product meets market demands. By understanding and embracing the nuances within this relationship, both designers and manufacturers can set the stage for innovative practices that enhance overall product efficacy.
Intro to Product Design in Manufacturing
Product design plays a crucial role in the realm of manufacturing. The connection between how products are conceived and how they are ultimately produced is often underestimated. This article will provide a clear view of this relationship, outlining the significance of effective product design practices in guiding the manufacturing process.
Defining Product Design
Product design can be understood as the process of creating and developing a product from initial ideas to finished comepting products. It encompasses several features, including usability, aesthetics, and functional aspects, prioritizing user needs. Designers analyze what consumers require and how they will interact with a product. This stage is fundamental. Understanding what to design influences every aspect of manufacturing.
A well-defined product design considers various factors, such as how users will feel about the product, which prototype materials will be needed for production, and how easily pieces can be manufactured at scale. Effective designs encapsulate user-centric approaches, ensuring that the end product meets sites or even exceeds market expectations.
Importance of Product Design in Manufacturing
Product design significantly impacts each stage of the manufacturing process. First, it establishes standards for quality, efficiency, and practicality.
Effective product design directly contributes to streamlined operations, reducing production time and costs.
The ways product design affects manufacturing include:
- Efficient Material Use: A good design prevents excess or waste in production phases.
- Enhanced Functionality: Design choices influence performance. Well-crafted products meet or exceed user expectations.
- Cost Reduction: Thoughtful designs minimize alterations needed later in the process, potentially saving resources.
- Market Competitiveness: Along with aesthetics and user engagement, well Oververse product design factors into brand reputation.
Within manufacturing, success often leans heavily on the design's initial developmental stage. Without it, the manufacturing chain suffers from inefficiency and increased ineffective costs. Hence, staff engage in reconsidering designs to ensure expecations are meet or avoided totally. This continued effort signals an embrace on the necessity of robust product design in fostering effective manufacturing approaches.
The Design Process
The design process plays a critical role in manufacturing, serving as the foundation for how a product comes to life. It encompasses various phases, ensuring that a project evolves from vague ideas to concrete solutions that meet both functional and market demands. Final outcomes depend wholly on the way designers navigate this landscape, which is often both complex and nonlinear. Key elements of the design process include systematic planning and iterative methodologies that encourage refinement through feedback.
Stages of Product Design
Concept Development
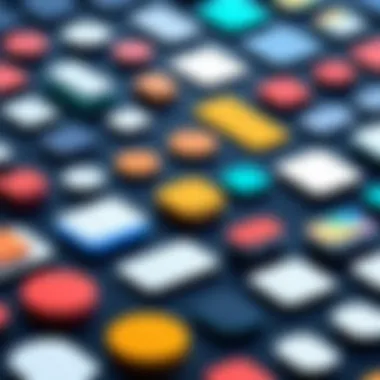
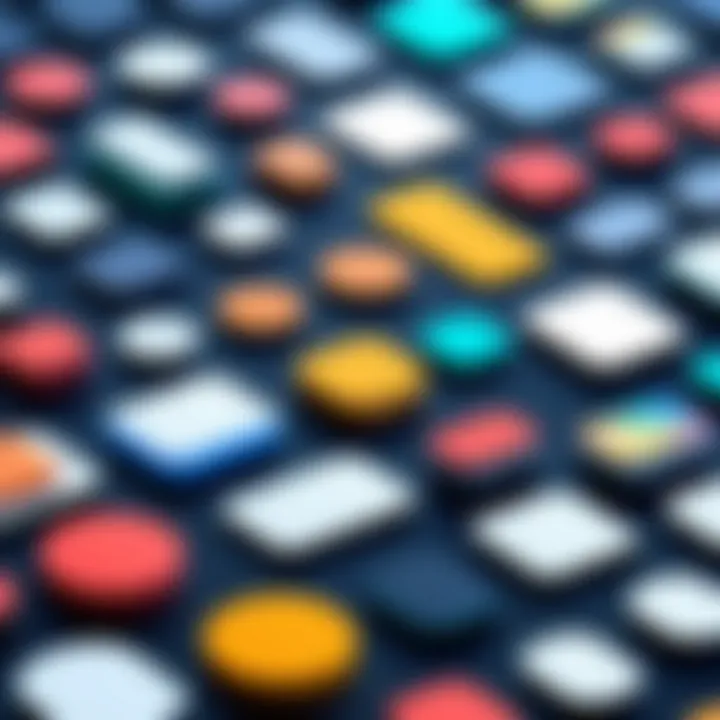
In concept development, teams brainstorm and outline ideas that address specific market needs. This phase is essential as it sets the direction for subsequent stages. The significance of this initial phase can not be overstated; it allows for unfiltered creativity and the exploration of possibilities without tangible constraints. Hence, the final selections must align with market trend or user needs.
A key characteristic of this stage is its non-linear nature. Ideas can shift directions quickly, allowing flexibility that can foster innovation. It is a beneficial choice for this article because this initial brainstorming influences the entire design trajectory, and thus, relating products directly to consumer needs.
However, a unique feature of concept development lies in its time investment; if not managed well, these phases can overrun schedules, leading to wasted resources and missed opportunities.
Prototyping
Prototyping is the next crucial part, conducting the tangibility of ideas. By creating early models, teams can assess both aesthetics and functionality. The contribution it makes is pivotal. Prototypes serve as interactive tools, allowing stakeholders to visualize concepts in action.
The key characteristic here is the ability to identify potential flaws before entering the manufacturing phase. This can be of significant benefit, as rectifying issues during prototyping is generally less costly compared to revising at production. Prototypes can vary in fidelity, from paper sketches to 3D models, which often impacts the depth of feedback received.
Despite these advantages, a potential disadvantage exists. Prototyping consumes resources and time, and an excessive number of iterations can stall projects rather than making tangible progress, demanding careful management and scheduling.
Testing and Evaluation
The testing and evaluation phase serves to verify that designs indeed perform up to expectations. By rigorously examining the prototypes against predetermined metrics, questions of relevance, durability, and user-friendliness are resolved. Its role in this context cannot be under-appreciated as it establishes whether the design fulfills its original intent before it goes to production.
This stage’s key characteristic is its data-driven approach. Through quantitative feedback, teams gather critical insights necessary for informed design tweaks. The push for quantifiable results reaffirms the practice’s popularity as it safeguards against failure risk. Designs undergo multiple iterations here to allow focus on user feedback therefore validating concept through practical experience.
However, it can stall progress if overly tightly linked to rigid assumptions about how users will interact with the product in real-world conditions. It requires capturing thorough input to avoid just reiterating existing user biases.
Interdisciplinary Collaboration
Engineering and Design
Interdisciplinary collaboration connects design with engineering directly affecting product outcomes. Close teamwork allows for seamless interaction between aesthetic values and functional specs. This cooperation ensures both sides keep each other in check for better overall quality efforts.
The marrying of creativity with practicality is central to this phase’s significance. Decision-making becomes robust, as engineering insights inform design iterations and vice versa. It greatly enhances efficiency, ultimately benefiting the manufacturing phase as the final product is thoughtfully engineered with its intended market behaviors in mind.
However, the potential conflict may arise between aesthetic desires and engineering limits and unless this is well managed, it might delay product releases.
Marketing Insights
Integrating marketing insights is equally key. By presenting data about expectations and competitive landscapes, designers can produce work that resonates strongly with intended consumers. It creates demand and reinforces commercial viability, achieving genuine market alignment through scholarly and quantitative analysis. Understanding the buying public assists designers to make informed decisions throughout the process.
A distinctive feature of this collaboration is it leans towards representational analytics—include surveys, focus groups, and selling trends ensure increased design relevancy which attributes value directly back to the market stake.
Yet, incorporating marketing too late can lead interplay of goals being missed; one weakness here could become design compromise for needs aligned solely on market pressures without fosters strategic innovation. Therefore, integration should begin early in the design process.
Design for Manufacturability
Design for Manufacturability (DfM) is a crucial principle in the field of product design, particularly in manufacturing. It focuses on simplifying the product design so that it can be easily and cost-effectively manufactured. The main goal is to optimize the compatibility between the design and production processes to help achieve an efficient workflow. Engagement with DfM helps bridge the gap between engineering and manufacturing teams. By doing so, companies can improve the quality of products while reducing production times and costs.
Considerations of DfM include selecting appropriate materials that align with the design choices and the manufacturing processes. Each decision in this phase can significantly influence production efficiency. Proper integration often results in streamlined processes, reducing the need for rework. Companies that adeptly apply DfM will likely respond more adeptly to market demands and customer needs.
The importance of this approach is not only in the direct correlating expenses and efficiency, but it also fosters innovation and systematic thinking within teams. Ultimately, prioritizing manufacturability leads to strengthened products and competitive advantages in the market, reinforcing the organization’s success in navigating shifting business environments.
Principles of Design for Manufacturability
When discussing design for manufacturability, it is essential to address several fundamental principles that contribute to its effective implementation. These principles include:
- Minimizing Part Count: A simplified design with fewer components can dramatically decrease assembly time and costs.
- Standardizing Components: Using standard parts and materials wherever possible can help reduce manufacturing complexity.
- Designing for Easy Assembly: The product should be easy to assemble, thereby minimizing the risk of errors and reducing labor time.
- Incorporating Tolerances: Smart choice of tolerances inline with manufacturing capabilities can lower costs and improve fit and function.
- Considering Manufacturing Techniques: Understanding resource limitations and suitable manufacturing techniques early field leads to improved product designs more aligned with feasible production processes.
By adhering to these principles, businesses can minimize overhead costs while promoting efficiency, ultimately empowering designers and engineers to create better products for consumers.
Impact on Production Costs
The implications of design for manufacturability extend significantly into production costs. When designs are suitable for manufacturing by merit of their inherent characteristics, costs can be driven down in various ways:
- Reduced Material Waste: Thoughtful design minimizes waste during both production and assembly.
- Faster Production Times: If components are simple to manufacture and assemble, overall timing decreases, maximizing productivity.
- Lower Labor Costs: Product designs that reduce complexity can lead to less required labor for tasks such as assembly and fitting.
- Decreased Rework and Scrap Rates: Effectively integrated designs can mitigate mistakes, leading to fewer defects that necessitate rework.
- Enhanced Supply Chain Efficiency: A focused approach on manufacturability ensures upstream suppliers are considered, helping in achieving streamlined sourcing and logistics.
Understanding the impact DfM can have on production costs helps illustrate the frictionless connection between effective product design and manufacturing. This understanding allows for both practical and strategic decisions and changes within companies aiming for growth and better competitive positioning.
Material Selection and Design
Material selection plays a vital role in product design and manufacturing. It holds implications for performance, cost, and sustainability of the final product. Selecting the right materials can not only enhance product quality but also improve manufacturability. Considering the right materials starts right from the design phase, influencing everything from production processes to customer satisfaction.
Factors Influencing Material Choices
When selecting materials for product design, multiple factors come into play. These include:
- Mechanical properties: Strength, flexibility, and durability need a careful balance. Products require materials that can endure operational demands without financial constraints.
- Cost considerations: Cost-effectiveness is critical. While some materials might offer exceptional qualities, the total expenditure needs to be justified in the context of market expectations and profit margins.
- Manufacturing techniques: Some materials are more compatible with specific production processes. Understanding how materials behave during fabrication is important for smooth workflow and minimizes defects.
- End-user requirements: User needs can dictate material choices. Different applications require materials with specialized properties to ensure that the product meets functional requirements.
An informed decision about these aspects leads to better sustainable choices which reflect on overall product design.
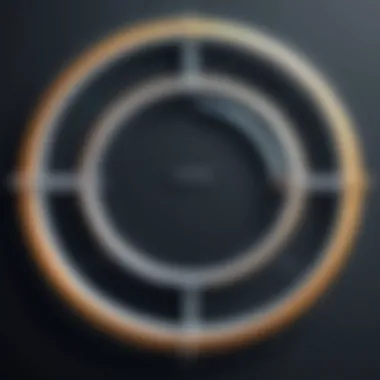
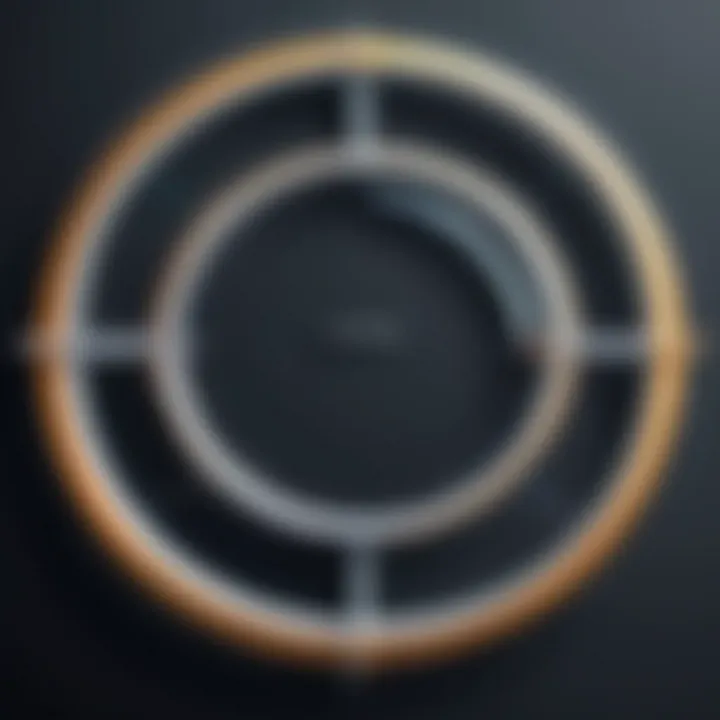
Sustainability Considerations
Sustainability has increasingly become a critical factor in product design. Designers and manufacturers are noticing that consumer preferences are shifting towards environmentally responsible choices. Important considerations include:
- Recyclability: Selecting materials that can be recycled contributes to reducing waste. This efficiency is beneficial for the environment as well as long-term cost savings for manufacturers.
- Bio-based materials: Using plant-based and other renewable resources is gaining attention. These materials minimize dependence on fossil fuels and reduce the carbon footprint associated with production.
- Life cycle assessment: Evaluating the environmental impact of materials throughout their entire life cycle is paramount. The goal is to minimize resource consumption, energy use, and waste at every stage, from extraction to disposal.
Understanding sustainability helps companies not only meet compliance requirements but also cater to consumer demand for eco-friendly products.
Technological Integration in Design
The integration of technology into product design is not just beneficial, but essential in today’s manufacturing landscape. Technological advancements have redefined how designs are envisioned, developed, and implemented. The incorporation of tools and techniques reshapes the workflow. It enhances creative possibilities while driving efficiency.
Technology provides tools that make the complexities of product design more manageable. This transmutes abstract ideas into tangible plans quickly and accurately, allowing designers to explore more options within a shorter timeframe. The utilization of sophisticated technologies promotes innovation, enabling designs that were once impractical or impossible.
The Role of CAD Software
Computer-Aided Design (CAD) software stands at the forefront of technological integration. This tool plays a pivotal role in streamlining the product design process. CAD allows designers to create precise drawings and models quickly. It significantly simplifies the editing process. Mistakes can be corrected rapidly without the need for physical prototypes.
Benefits of CAD include:
- Enhanced Accuracy: CAD eliminates many human errors.
- Improved Communication: Clear designs can be easily shared among stakeholders.
- Efficiency: Designers can save time on developing complex figures.
Thus, CAD software establishes a strong foundation for product designs in manufacturing.
Emerging Technologies
Emerging technologies play an integral role in modern product design. These innovations are transforming traditional manufacturing processes and introducing new methodologies.
3D Printing
3D printing revolutionizes how products are manufactured. This technology enables the creation of complex structures layer by layer. The key characteristic of 3D printing is its ability to produce prototypes rapidly and at a lower cost.
Advantages of 3D printing include:
- Cost-effectiveness: Reduces waste and lowers material costs.
- Flexibility: Facilitates customization of designs based on user feedback.
Nonetheless, 3D printing has its drawbacks. It may not always produce items as strong compared to traditional methods. There are still limitations regarding material choices and scaling production.
Artificial Intelligence
Artificial Intelligence (AI) is becoming increasingly common in product design. This technology helps analyze massive sets of data to conclude upcoming patterns and consumer preferences. The crucial element of AI is its predictive capability.
AI’s unique feature involves automation in decision-making processes. This leads to more effective product design lifecycles. The advantages of AI integration include:
- Enhanced Design Accuracy: Minimize errors in design.
- Speed: Accelerate development times and bring products to market faster.
However, there are concerns as well. Relying too heavily on AI might diminish human creativity and intuition in the design process.
The integration of these technologies impacts efficiency, innovation, and the capability to meet modern consumer demands.
Feedback Loops in Product Design
Feedback loops are essential components in product design. They enable firms to refine their development processes through insights and reactions from users. The significance of these loops cannot be overstated, as they foster a culture of continuous improvement. When designs align with real-world user experiences, the likelihood of a product's success increases markedly. Understanding the mechanisms of feedback loops aids in how designs can be effectively adapted during various stages of the product life cycle.
Collecting User Feedback
Effectively collecting user feedback involves multiple methodologies. Surveys and interviews are among the most common. They provide deep insights into user experiences, revealing what does and does not work. For instance, utilizing platforms such as Reddit can generate valuable discussions around user perceptions. Moreover, analyzing user data from apps enables identification of patterns in usage. Tools like Facebook's sentiment analysis also assist in gauging public opinion.
User testing sessions can be arranged to gather direct inputs. Observing how users interact with a product can unveil areas for enhancement that designers may overlook. These engagement methods are vital, offering insight directly from users engaged with the product often. Organizing focus groups allows designers to probe deeper, examining specific elements in more detail. Hence, comprehensive collecting processes will ultimately lead to high-value modifications.
Iterative Design Processes
Incorporating iterative design processes allows teams to evolve a product through cycles of modifications based on feedback. Each iteration leads to an improved understanding of user needs and enhances overall design quality. By systematically integrating user feedback, the iterative process helps in addressing concerns earlier in development. This step-by-step enhancement avoids larger deviations late in product timelines.
Changing a product's direction in response to feedback encourages flexibility and innovation. As team members discuss insights from users, brainstorming alternatives may emerge, guiding further refinement. Different stages of the design process can utilize iterations, from concept to testing. Timely pivots infused by actual user feedback can make a notable difference.
Continuous learning is intrinsic to successful product design. Each feedback loop serves not only to validate design decisions but also instigates innovation.
The interaction cycles strengthen relationships between designers and users, ensuring that products evolve alongside user expectations. Therefore, implementing feedback mechanisms throughout is not just valuable but essential in today's competitive landscape.
Case Studies of Successful Product Design
The analysis of case studies in successful product design plays a crucial role in understanding how effective design translates into meaningful production outcomes. These studies provide empirical evidence regarding best practices, innovation outcomes, and potential pitfalls in the design process. Evaluating variuos case studies gives insights into the specific elements and benefits that contribute to successful product design in the manufacturing landscape.
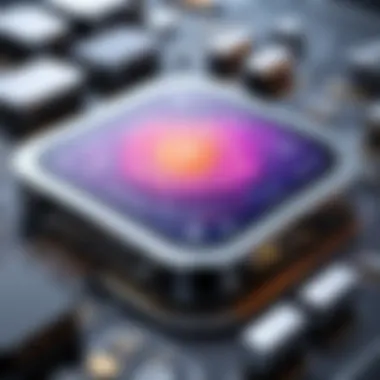
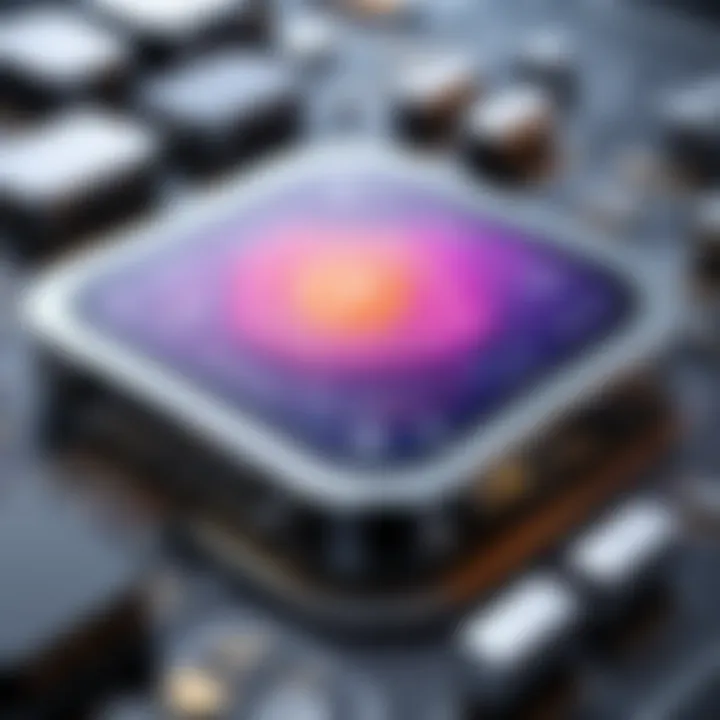
Through these lenses, significant patterns emerge that can act as guidelines for designers and manufacturers alike. These examples serve to demonstrate not only the techniques applied but also how responsive design can help adapt products to market needs and consumer behavior.
Innovations in the Automotive Industry
The automotive industry has frequently been at the forefront of product design innovation. Reports indicate that brands like Tesla have altered how consumers view electric vehicles.
Design innovations include:
- Streamlined manufacturing processes where components are designed for multiple vehicle models.
- Technology integration, like infotainment systems, that directly address consumer needs for connectivity.
- Sustainability and recyclable materials used for car interiors, reflecting growing environmental concerns.
In this case, the focus on user experience redefined how products in the automotive sector are conceived and function. The design elements incorporate advanced safety features, efficient fuel consumption, and intelligent interfaces, ushering the industry into a tech-enabled era, where design is about much more than aesthetics.
The advancements made in workforce productivity through voluntary education programs and collaboration with designers ensure that innovations continue moving forward. The use of simulation tools allows off-road trials to occur before the prototype stage. The feedback loop in design thus shortens, improving product quality rapidly.
Consumer Electronics Breakthroughs
Consumer electronics such as smartphones and laptops demonstrate another critical facet of effective product design. Companies like Apple and Samsung lead through aggressive innovation strategies, which provide rich examples relevant to this discussion.
Breaking down achievements in this sector reveals:
- User-centric design, prioritizing features based on thorough research and consumer behavior analysis.
- Seamless integration of hardware and software, allowing for intuitive user interface experiences.
- Continued adaptation to evolving societal norms, such as reduced device sizes without compromising performance.
This industry thrives on fast-paced changes. Consequently, designers often cycle through each phase of product design multiple times to stay ahead. It reflects why continuous feedback loops and market agility are vital. Failure to project new consumer preferences with respect to emerging technological innovations can yield devastating consequences for brands.
Exploration of case studies has become essential, demonstrating where design fails and succeeds. It's an ongoing cycle of improvements based on tangible results and market adaptivity.
To conclude, examining case studies of successful product design not only validates theoretical concepts but also offers pragmatic insights into real-world applications. The car and consumer electronics sectors present significant lessons in understanding how and why effective product designs can reshape markets and create lasting consumer value.
Challenges in Product Design for Manufacturing
The relationship between product design and manufacturing is not without its challenges. Understanding the nuances of these challenges is essential for organizations aiming to innovate while maintaining cost-effective production processes. This section will elaborate on the crucial elements involved in navigating the complexities of product design in the manufacturing sector.
Overcoming Design Constraints
Design constraints can stem from various sources, including material limitations, regulatory standards, and production capabilities. Recognizing these limits early can significantly influence a successful product design. By actively engaging with engineers, designers can gain insights into the practical feasibilities of their concepts. Moreover, utilizing tools such as Computer-Aided Design (CAD) software allows for real-time simulations, highlighting potential issues prior to committing to physical prototypes.
Considerations for overcoming these constraints are critical. A few areas to focus on include:
- Material compatibility
- Environmental regulations
- Safety standards
- Production capabilities
By factoring these points into the initial design stages, companies can adapt their ideas accordingly, fostering innovations that remain grounded in what can be realistically manufactured.
Additionally, close collaboration with suppliers can lead to alternative solutions that might overcome specific limitations. Effective communication often results in discovering better materials or techniques that enhance design capabilities.
Balancing Innovation and Cost
In today’s manufacturing landscape, striking the proper balance between innovation and cost is more important than ever. Innovative designs may promise tremendous value to users, yet they can also inflate production costs. Understanding this balance allows companies to make strategic choices that either embrace market-leading technologies or stay within manageable budgets.
The following factors can help manage the interplay between innovativeness and the financial overhead of production:
- Value engineering: Analyze where costs can be reduced without sacrificing the quality of the final product, allowing designers to explore creative options inside a viable financial framework.
- Market research: Understand consumer preferences to ensure the pursued innovation aligns with actual demands. This method offers visibility into areas most likely to succeed.
- Fast prototyping: Utilizing technologies like 3D printing can speed up the sample creation process while also keeping costs low. This method can support advanced design options and rapid iterations based on consumer insights.
Overall, successfully balancing these two factors results in a product that meets consumer needs while maintaining profitability for the manufacturer.
In essence, challenges in product design for manufacturing compel teams to cultivate a culture of creativity and practicality to enhance innovation while being considerate of cost.
Exploring these challenges in product design sheds light on the some key concerns of modern manufacturing ahead. Awareness of open issues ensures that strategic solutions are carefully considered and implemented effectively.
Future Trends in Product Design and Manufacturing
The exploration of future trends in product design and manufacturing holds great significance. Understanding these trends provides insights into how innovations will affect creativity, effectiveness, and efficiency in the industry. Factors like technological advancements and shifts in consumer behavior drive these trends. The evolution doesn't simply enhance productivity, but it also reshapes the core values of design itself, balancing functionality with aesthetics and sustainability.
The Evolution of Smart Manufacturing
Smart manufacturing encapsulates the integration of technology and automation into design. This evolution allows manufacturers to make data-driven decisions throughout the product cycle. The utilization of Internet of Things (IoT) devices enhances real-time feedback loops between design and production.
Key components include:
- Automation: Robots and automated systems ensure consistency and reduce human error in manufacturing. This consistency improves overall quality.
- Data Analytics: Continuous data collection provides analytics to adjust processes as necessary, optimizing production with expedience.
- Interconnected Systems: Seamless integration connects every step in the production chain—from design to end-user interactions. This approach results in a responsive manufacturing environment.
Smart manufacturing changes expectations not only for efficiency but also for innovation. Design teams must now consider how their products will operate within fully automated systems, presenting opportunities to provide smarter, refined functions beneficial to users.
Anticipated Changes in Consumer Preferences
As people become increasingly conscious about their purchasing decisions, consumer preferences are poised to shift notably. Design must respond to these transformative expectations to maintain relevance in an evolving market. The emphasis on sustainability and personal connection personalization directly impacts product design choices.
Predicted shifts include:
- Sustainability: A growing number of consumers prioritize eco-friendly products. Design strategies must integrate sustainable materials and emphasize circular economies, where products are created, used, and returned to their original state.
- Customization: Shoppers seek unique products tailored to their preferences. The trend towards customizability in design can differentiate products in a saturated market.
- User Engagement: Consumers desire brands that engage them interactively. Involving users in the design process enhances connection and satisfaction.
Understanding these changing preferences is imperative. They represent not just a trend but a fundamental shift towards responsible consumption.