Understanding Gemba: The Key to Lean Management Success
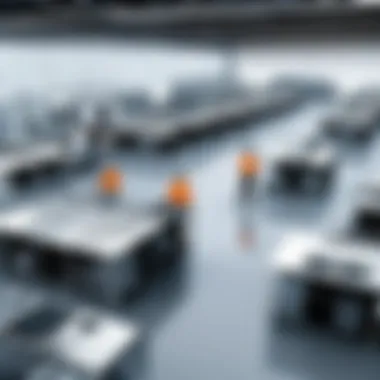

Intro
Gemba is a fundamental concept in the principles of lean management that guides organizations in improving processes, minimizing waste, and fostering a culture of continuous improvement. The term originates from Japanese, meaning
Defining Gemba
The concept of Gemba is critical to lean management. It emphasizes the importance of being present at the workplace. By observing processes in person, leaders and employees gain insights into real work conditions. This familiarity helps in identifying necessary improvements. The focus is not just on data or reports; it starts from the actual site where value is created.
Origin and Etymology
Gemba originates from the Japanese word, which means
Significance of Gemba
The concept of Gemba holds a vital place in the realm of lean management. Its significance comes from its practical approach to decision-making and continuous improvement processes. By focusing on engaging with actual work processes rather than abstract theories, organizations promote a culture of integrity and reality. Gemba facilitates a bottom-up approach where employees at all levels can contribute effectively to improvements.
Understanding Workplace Realities
Knowing the real scenarios within the workplace is prudent for any organization aiming for efficiency. Gemba emphasizes the value of direct observation in this understanding. Management often possesses insights concerning strategies and goals; however, to grasp actual workplace challenges requires physical presence at the Gemba, or the
Gemba Walks
Gemba Walks are vital components of the Gemba philosophy. They represent active engagement with processes by going to the place where work occurs. This hands-on approach fosters a direct understanding of operations, enabling leaders to observe and evaluate workplace realities, which is crucial for continuous improvement. Through Gemba Walks, organizations can shed light on inefficiencies and enhance communication among team members.
Purpose and Objectives of Gemba Walks
The main purpose of Gemba Walks is to gather first-hand information about processes, tasks, and employees’ experiences. By walking to the workplace, leaders and managers can:
- Identify Waste: Finding areas where resources may be wasted or underutilized.
- Foster Accountability: Engaging with employees fosters a culture where accountability is prized.
- Enhance Collaboration: Conversations during these walks promote team cohesion and collaborative problem-solving.
- Improve Processes: Observations lead to insights, helping teams develop solutions that drive efficiency.
As a result, Gemba Walks encourage openness and authenticity in the workplace environment, creating healthier communication dynamics.
Steps to Conduct a Gemba Walk
Conducting a Gemba Walk is systematic. The following steps should ideally be followed:
- Preparation: Set objectives for the visit and inform team members.
- Go to the Gemba: Physically move to the place where work is done.
- Observe Carefully: Take time to watch how employees perform their tasks without intervening initially.
- Engage with Employees: Ask open-ended questions to gather insights about their experience.
- Identify Areas for Improvement: Discuss observations and determine which processes can be improved.
- Follow Up: Ensure that the findings lead to actionable solutions and monitor improvements.
By structured approach, the value derived from these walks is maximized, resulting in real performance enhancements.
Best Practices for Effective Observation
To make Gemba Walks fruitful, consider incorporating the following best practices:
- Listen Actively: Encourage team members to express their thoughts and experiences.
- Remain Open-Minded: Don’t go in with preconceived notions, be open to learning the realities of the workplace.
- Take Notes: Document your observations to reference later.
- Respect the Workspace: Avoid interrupting workflows to minimize disruption within teams.
- Welcome Feedback: Post-walk discussions are essential. Invite employees' feedback on the walk to understand their perspectives better.
Core Principles of Gemba
Understanding the core principles of Gemba is vital for organizations looking to enhance their operational processes. These principles underpin the Gemba philosophy and direct organizations toward improved efficiency and learning. Utilizing these key tenets can result in a tranformation of the workplace culture, propelling organizations to meet their objectives effectively.
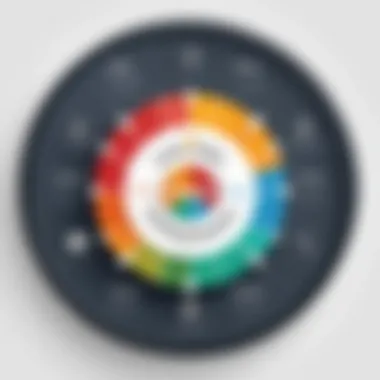

Value Stream Mapping
Value Stream Mapping (VSM) is an analytical method used to visualize and optimize processes in a particular workflow. It aids in identifying inefficiencies, waste, and delays in the creation of a product or service. The primary objective of VSM is to see every step of the cycle, from the inception to the final steps. Benefits of using value stream mapping include:
- Identification of Boost Areas: VSM helps organizations realize where daily activities cause bottlenecks. This way, companies can streamline processes, remaining flexible to customer needs.
- Concrete Actions: By visualizing the whole production line, employees can recognize specific areas that require change.
- Enhances Awareness: A visual mapping creates understanding among team members about their roles in the overall flow of work.
Continuous Improvement (Kaizen)
Continuous Improvement, commonly referred to as Kaizen, is rooted in the philosophy of ongoing, incremental improvements. This principle emphasizes small, regular changes that contribute to efficiency gains over time. Kaizen is particularly useful for fostering a culture of proactive problem-solving. Key points include:
- Empowerment of Employees: The essence of Kaizen lies in drawing on collective input from employees at all levels. When individuals feel empowered, they develop a personal stake in improvement.
- Feedback Loops: It establishes a systematic approach to gathering feedback and harnessing insights for the continuous growth and development of processes.
- Sustainability: Kaizen’s emphasis on gradual processes avoids the potential pitfalls associated with large-scale operations that may disrupt current workflows.
Respect for People
Respect for People is perhaps one of the most significant principles under the Gemba philosophy. It centers on creating a supportive environment where everyone’s voice is valued. This principle highlights not only personal respect but also considers the needs and aspirations of the workforce. Important aspects include:
- Creating Trust: Building relationships based on trust motivates a workforce to engage fully, contributing their insights toward improvement.
- Essential Communication: Respect engenders open communication channels, ensuring that employees share ideas and concerns freely.
- Impact on Culture: This principle fosters inclusivity, creating a workplace environment focused on collaboration and shared success.
Given the emphasis on progress and refinement in all areas of business, integrating these core principles of Gemba enables organizations to adopt a strategic approach toward sustainability and successful change.
A focus on values like respect, continuous improvement, and streamlining flows leads to organizations better adapted to modern operational challenges.
Implementing Gemba in Organizations
Implementing Gemba in organizations is crucial for enhancing operational efficiency and fostering a culture of continuous improvement. The focus on Gemba encourages leaders and employees to engage with the working environment, observe processes in real time, and identify areas that need enhancement. This understanding transforms not only the workflow but also the mindset of the workforce.
Identifying Opportunities for Gemba
To harness Gemba effectively, organizations first need to identify specific opportunities where Gemba practices can be applied. This can involve examining various processes within an organization to pinpoint inefficiencies or areas for improvement. For example:
- Bottlenecks in Production: Identify stages causing delays in the production line.
- Quality Control Issues: Look for patterns in product defects or service failures.
- Employee Feedback: Gather suggestions from frontline workers, as they often have keen insights on process flaws.
- Customer Interactions: Observe areas where customer complaints originate, indicating a lack of efficiency or quality.
By recognizing these opportunities, companies can plan effective Gemba activities that yield meaningful improvements.
Training Employees on Gemba Principles
Training employees on Gemba principles is vital to ensuring successful implementation. Employees must understand the value of direct engagement in their daily roles. The training can be structured into several key areas:
- Understanding Gemba Philosophy: Workers should learn the basic tenets of Gemba and its significance in lean management.
- Observation Techniques: Teach employees how to observe processes critically and analytically.
- Effective Communication Skills: Emphasizing open communication during Gemba walks allows for constructive dialogue between employees and management.
- Continuity in Improvement Practices: Establishing regular reviews of previous Gemba findings keeps the momentum alive.
Education in these areas not only helps employees feel empowered but is also a strong step toward integrating Gemba habits into the company culture.
Challenges and Misconceptions about Gemba
Gemba is often seen solely as a tool for enhancing operational efficiency. However, understanding its challenges and misconceptions is vital for implementing it effectively in an organization. This section addresses the frequently encountered misunderstandings and barriers to adoption. Knowing these factors can shape a better approach to integrating Gemba into workplace practices.
Common Misunderstandings
Several misconceptions cloud the concept of Gemba. Some individuals mistake Gemba for mere physical presence on the shop floor. They think that simply walking around will suffice. In reality, a Gemba walk is not just about being onsite; it requires active engagement and observation, ensuring the focus is on identifying problems and opportunities for improvement.
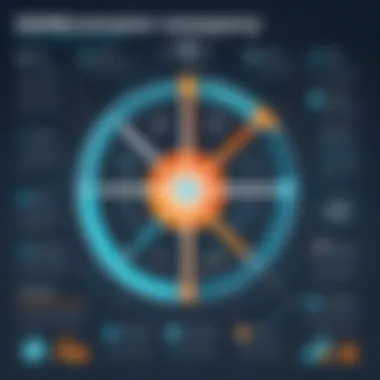

Another misconception is viewing Gemba exclusively as a management tool. This perspective often alienates employees on the front lines. Gemba is, in fact, a philosophy aimed at fostering a culture of collaboration. It's important for employees at all levels to participate actively in Gemba initiatives for maximum benefit.
Moreover, some managers believe that Gemba is a quick-fix solution. Misinterpreting it this way can lead to frustration. True implementation of Gemba principles takes time, trial, and reflection. Lasting change occurs over continuous iterations rather than through a rapid overhaul.
Overcoming Resistance to Gemba Practices
Resistance to Gemba practices may emerge from employees and managers who fear change. To address this resistance, organizations must communicate the benefits clearly. When team members grasp how Gemba principles can streamline processes, enhance teamwork, and eliminate waste, readiness to embrace the practice increases.
Training is another vital component. By providing proper education about Gemba, organizations reduce misunderstandings. Workshops and ongoing training sessions create a strong foundation for practice. Empowering the employees gives them confidence to engage actively during Gemba walks.
Listening to feedback is also crucial. Feedback allows ground-level employees to share their insights, which might be used to refine Gemba practices. Incorporating their suggestions will foster an atmosphere of mutual respect and understanding within the organization.
In short, tackling challenges and misconceptions in Gemba implementation is essential for cultivating an effective continuous improvement mindset in the workplace.
Establishing a strong communication framework is key. Sharing success stories from within the organization helps illustrate practical benefits of Gemba. These stories can further convince skeptics and resonate with other stakeholders. Overall, clear and consistent communication paves the way for smoother adoption of Gemba principles.
Gemba in Different Industries
Understanding how Gemba is applied in various industries underscores its adaptability and relevance across diverse organizational contexts. The practical implementation of Gemba principles can drive improvements and streamline processes, leading to enhanced operational efficiency, regardless of the industry framework. The importance of this concept hinges on a nuanced approach that accommodates specific challenges and opportunities inherent in each sector.
Manufacturing Sector
In the manufacturing sector, Gemba takes center stage as a vital strategy for operational excellence. The concept emphasizes going to the source where products are created to identify inefficiencies and explore opportunities for improvement. A significant benefit of Gemba in manufacturing is the reduction of waste through direct observation of workflows and processes.
- Key elements in Gemba for manufacturing involve:
- Establishing clear metrics for performance evaluation.
- Involvement of key stakeholders; from frontline workers to management, collaboration enhances the robustness of solutions.
- Real-time problem resolution ensures timely actions are taken to avoid further detriment in production lines.
By integrating Gemba practices, manufacturers not only enhance productivity but also strive for a culture of continuous improvement (Kaizen), promoting employee engagement in identifying areas for enhancement.
Healthcare Applications
Adopting Gemba principles in the healthcare sector can lead to significant advancements in patient care quality and operational efficiency. By observing patient flows and processes firsthand, healthcare professionals can gain invaluable insights into where inefficiencies occur. This direct engagement cultivates an environment where constant improvement is not only encouraged but embedded in daily practices.
- Some benefits of Gemba in healthcare include:
- Improvement in patient safety through analysis of procedural compliance.
- Enhanced communication among teams as they observe procedures together.
- Optimized resource utilization, ensuring that medical supplies and personnel are aligned with patient needs effectively.
Healthcare applications of Gemba emphasize aligning processes with patient experience, ultimately resulting in improved outcomes.
Gemba in Service Industries
Gemba's influence reaches into service industries as well, where service delivery and customer satisfaction comprise the forefront of operational success. Service businesses often rely on direct interactions with clients; thus, Gemba proves instrumental in understanding and refining these interactions. It helps businesses grasp customer perspectives, thereby crafting notably improved experiences.
- Important considerations when applying Gemba in service industries include:
- Focusing on front-line staff feedback, as they are the first touchpoint for customer service.
- Mapping service delivery processes to identify bottlenecks.
- Developing consistent metrics for evaluating customer satisfaction.
Within service industries, the effectiveness of Gemba emerges from its capacity to harness employee insights that directly correlate with enhanced customer service experiences.
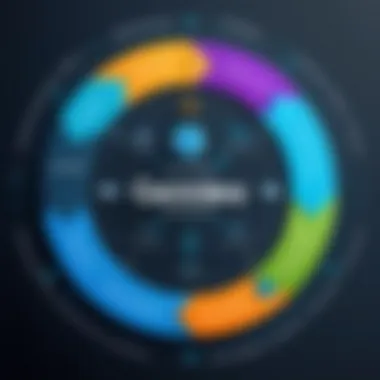

Continuous engagement with Gemba principles in various industries fortifies organizations with the tools to innovate and thrive in their respective markets.
Case Studies: Successful Gemba Implementation
The analysis of case studies plays a vital role in understanding the real-world impact of Gemba. It is through examining these examples that readers can appreciate the tangible benefits Gemba offers across various sectors. By investigating specific instances of successful Gemba implementation, we reveal how organizations have used the principles of Gemba to solve problems, streamline processes, and implement change effectively. The lessons learned from unipuent articles can inform future applications of Gemba in different contexts.
Moreover, these case studies provide a framework for assessing the scalability and adaptability of Gemba practices. They illustrate how principles applicable to one industry can be modified for another. In essence, case studies serve as practical blueprints, showing what works, what doesn't, and the nuances involved during implementation.
Global Manufacturing Companies
Global manufacturing companies have long been leaders in adopting Gemba principles, owing to their complex operations and supply chain networks. Businesses like Toyota and General Electric embody the essence of Gemba with their focus on efficiencies and productivity. These companies continually assess their production processes by engaging with their workers in real-time, directly on the shop floor, to understand obstacles hindering workflow.
One notable example in Toyota involves their renowned 'Toyota Production System' (TPS). Lexus, a segment of Toyota, implemented Gemba rituals to identify and reduce waste in manufacturing. The team conducted regular Gemba walks, which led to enhancements in assembly line efficiency and reduced production cycle times.
Additionally, GE's commitment to Gemba includes utilizing Lean Six Sigma methodologies to address variability in their products. Their Gemba strategy focuses on collecting metrics wherever value is created, allowing for data-driven decisions that enhance manufacturing reliability and quality.
The takeaway from these companies illustrates how deeply integrated Gemba can be within large manufacturing enterprises. The emphasis on real-time engagement fosters deep collaboration among employees, instrumental for continuous improvement.
Innovations in the Healthcare Sector
Applying Gemba in the healthcare sector has seen innovative use of the concept in implementing patient-centered care. Healthcare leaders are actively participating in Gemba walks not only to facilitate improvement in service delivery but to directly engage with patients and healthcare staff.
One memorable instance comes from Virginia Mason Medical Center in Seattle. They used Gemba principles to rethink patient flow. By observing the actual experiences of patients and staff in real-time, they identified bottlenecks in emergency room processes. This led to a redesign that improved wait times and overall patient satisfaction.
Another prime example is at Mount Sinai Health System in New York City. They developed a Gemba training program focused on enhancing communication among medical staff, disciplines, and departments. By using practical simulations and Gemba walks, actionable insights derived here helped streamline patient care pathways.
Innovative adaptations of Gemba principles in the healthcare domain resulted in impressions that extend far beyond operational enhancements. The application of Gemba methods presents evident value in understanding patient experiences, creating a more robust healthcare environment that ultimately promotes quality care.
Both manufacturing and healthcare sectors highlight the need for direct engagement and observation to realize the full potential of Gemba. Recognizing specific problems in real time offers unmatched insight necessary for fostering meaningful change.
Gemba and Technology
Gemba, initially a simple concept rooted in understanding the real workplace insights, has now evolved to intertwine with technology. As organizations grow more reliant on data and digital tools, it is crucial to analyze how these advancements elevate the Gemba philosophy. Enhancing traditional Gemba principles through technology allows a more robust evaluation of processes and improvements.
Advancements in technology facilitate the application of Gemba in distinct ways. This spans from gathering data during Gemba walks to utilizing software tools that enhance observation and analysis. Moreover, embracing technology in this context aligns with the goal of making informed decisions based on insights derived directly from the workplace.
Gemba without technology can limit the scope of understanding workplace dynamics in today’s data-driven landscape.
Leveraging Data for Gemba Activities
Incorporating data within Gemba practices significantly enhances their effectiveness. Data-driven Gemba activities enable organizations to gather measurable metrics and analyze trends that occur on the ground. Here are some key elements that highlight the importance of leveraging data in Gemba activities:
- Real-time Insights: Utilizing data collection tools during Gemba walks incorporates real-time observations into the decision-making process. This fosters a more agile response to issues that may arise on the shop floor or in service environments.
- Improved Visibility: Aggregating quantitative data from various sources allows teams to visualize processes effectively. By tracking and analyzing key performance indicators (KPIs), organizations can spotlight inefficiencies and work collaboratively to resolve problems.
- Benchmarking Progress: Data helps in establishing benchmarks that inform future Gemba activities. With measurable information, organizations can assess improvements over time and identify best practices.
Techniques such as employing mobile data collection apps can streamline gathering information during Gemba activities. Such tools encourage seamless documentation of observations, providing a clearer approach to data analysis.
The Role of Software in Gemba Practices
Software applications enhance the traditional Gemba practices by introducing advanced functionalities that create a more organized framework for operations. Here’s how software impacts Gemba:
- Process Mapping: Software solutions can assist in mapping out processes visually. Utilizing flowcharts or digital Kanban boards provides clarity regarding workflows and identifies potential bottlenecks.
- Collaboration Tools: Cloud-based collaboration platforms enable teams to comment and share insights from Gemba walks, encouraging cross-departmental discussions that drive improvements.
- Data Analysis: Implementing software capable of analyzing the gathered data enables deeper investigation into operational efficiency. Organizations can discover root causes and track resolution paths effectively.
In applying technology within Gemba, training employees on how to use these tools ensures they harness the benefits fully. Combining traditional practices with modern tools contributes to a culture of continuous improvement.
Thus, the relation between Gemba and technology commands attention. Embracing these advancements answers the need for greater efficiency, encouraging organizations to rethink and reshape their practices continuously.