Unlocking Success: Essential KPIs for Optimal Production Management
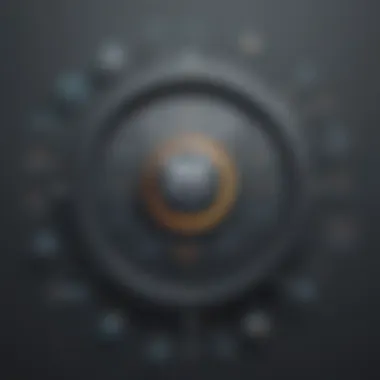
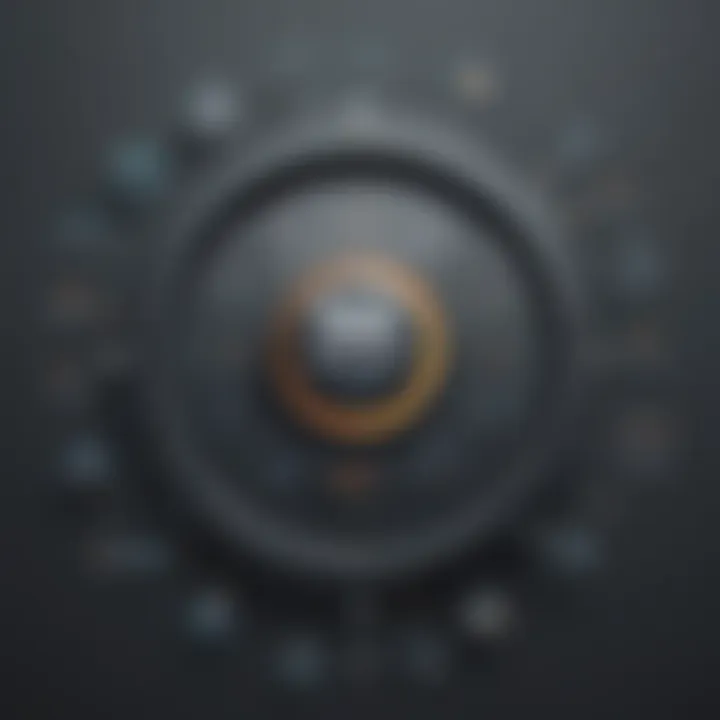
App Overview
In the realm of production management, optimizing efficiency and maximizing output are paramount goals. This article delves into the intricate web of key performance indicators (KPIs) essential for production managers. By scrutinizing these metrics, pivotal decisions can be informed, and processes can be fine-tuned to achieve peak performance levels.
Step-by-Step Walkthrough
When it comes to integrating KPIs into production management, a detailed understanding of each metric is imperative. From setting baselines to monitoring trends, every step plays a crucial role in enhancing operational effectiveness. Visual aids such as charts and graphs can aid in comprehending data patterns, facilitating informed decision-making in the pursuit of optimal outcomes.
Tips and Tricks
To master the art of leveraging KPIs, experts emphasize the need for a diligent approach. Regularly monitoring and analyzing KPI data can uncover hidden insights that drive efficiency gains. Implementing automation tools can simplify data gathering processes, allowing for real-time adjustments to enhance overall productivity.
Common Issues and Troubleshooting
While integrating KPIs into production management, potential challenges may arise. Understanding these hurdles is vital, as preemptive strategies can be devised to mitigate risks and optimize operations. Troubleshooting techniques, ranging from data verification to system audits, can address issues promptly, ensuring minimal disruption to workflow.
App Comparison
When comparing various KPI tools available in the market, it is essential to focus on distinctive features and functionalities. Contrasting the strengths and weaknesses of different applications enables production managers to make informed choices. By highlighting unique selling points, such as customizable dashboards or predictive analytics, decision-makers can select a KPI tool that aligns best with their organizational needs.
Introduction
Understanding Key Performance Indicators (KPIs)
Defining KPIs in Production Management
Defining KPIs in Production Management entails the meticulous identification of key metrics that quantify performance and progress within production processes. This aspect is quintessential as it sets the foundation for measuring success and establishing benchmarks for continuous enhancement. The unique feature of defining KPIs lies in its ability to offer a concrete framework for evaluating performance against set objectives, enabling production managers to pinpoint areas for refinement and development efficiently.
Importance of KPIs in Driving Performance
The importance of KPIs in driving performance cannot be overstated, as these indicators serve as strategic navigational tools that steer production operations towards success. By aligning KPIs with organizational goals, production managers can harness the power of data-driven insights to optimize efficiency and productivity. The significance of KPIs in driving performance lies in their capacity to provide actionable intelligence, empowering decision-makers to proactively address operational challenges and capitalize on growth opportunities effectively.
Role of Production Managers
Responsibilities and Challenges
The role of production managers encompasses a myriad of responsibilities and challenges that are integral to ensuring operational excellence. From overseeing production schedules to coordinating resources, production managers play a pivotal role in orchestrating the seamless execution of manufacturing processes. The key characteristic of these responsibilities lies in their direct impact on operational efficiency and product quality, making them a cornerstone of successful production management. While the challenges faced by production managers may vary, navigating through operational complexities, resource constraints, and demand fluctuations are common hurdles that require astute problem-solving skills and strategic decision-making.
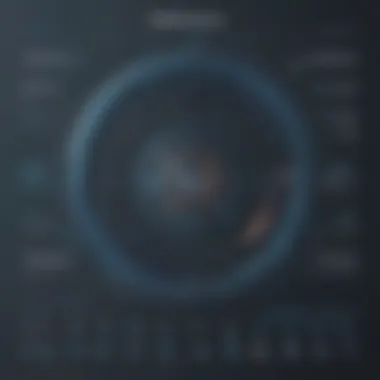
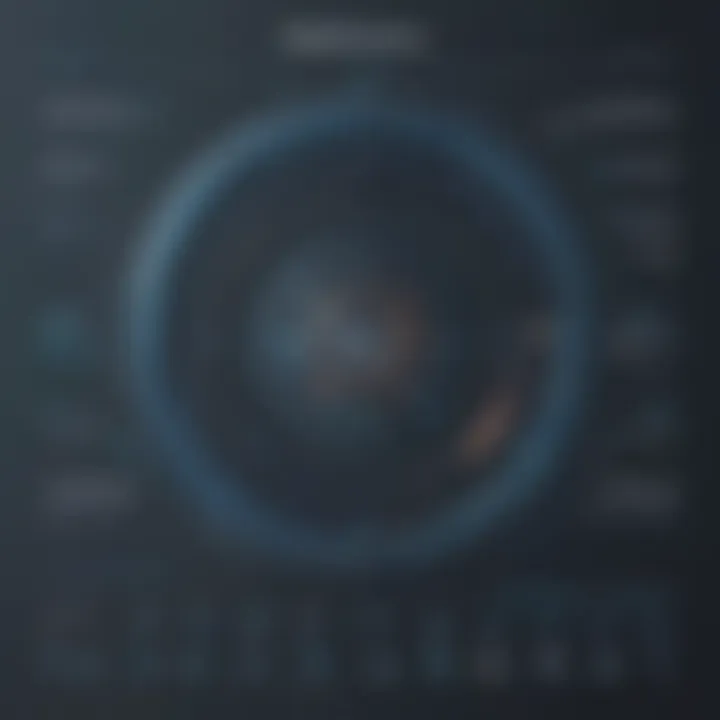
Impact on Overall Operations
The impact of production managers on overall operations is far-reaching, influencing not only the efficiency of production processes but also the bottom-line performance of organizations. By adeptly managing resources, optimizing workflows, and ensuring regulatory compliance, production managers contribute significantly to enhancing operational effectiveness and driving sustainable growth. The key characteristic of their impact lies in the ability to streamline operations, minimize bottlenecks, and foster a culture of continuous improvement, thereby solidifying the foundation for long-term success.
Significance of Performance Measurement
Implementing Metrics for Success
Implementing metrics for success is paramount in measuring the effectiveness of production processes and identifying opportunities for refinement. By deploying relevant KPIs and performance indicators, organizations can gauge the performance levels of various operational facets and make data-driven decisions to enhance efficiency. The unique feature of implementing metrics for success lies in the actionable insights they offer, enabling organizations to track progress, evaluate performance trends, and drive strategic improvements systematically.
Enhancing Decision-Making Processes
Enhancing decision-making processes through performance measurement empowers organizations to make informed choices based on real-time data and analytics. By leveraging KPIs to evaluate operational performance and quality metrics, decision-makers can enhance operational visibility, mitigate risks, and optimize resource allocation effectively. The unique feature of enhancing decision-making processes through performance measurement lies in the ability to align strategic objectives with actionable insights, fostering agility, and adaptability in the face of evolving market dynamics.
Key Performance Indicators for Production Managers
In the realm of production management, Key Performance Indicators (KPIs) serve as paramount tools to evaluate and improve operational efficiency. They offer precise insights into various aspects of production performance, enabling managers to make data-driven decisions. By delving into the specific elements of KPIs for production managers, this article sheds light on their significance in driving success and maximizing output. Effective KPIs not only monitor progress but also align operations with overarching organizational goals. Considerations about KPIs revolve around selecting metrics that are relevant, measurable, and reflective of the company's strategic objectives.
Efficiency Metrics
Efficiency metrics encompass critical parameters such as Overall Equipment Effectiveness (OEE) and Utilization Rate, which are instrumental in gauging production productivity. OEE measures the performance of equipment by accounting for availability, performance, and quality, providing a comprehensive view of manufacturing efficiency. This metric is popular due to its ability to pinpoint inefficiencies and guide improvement strategies effectively. Utilization Rate, on the other hand, indicates the extent to which resources are utilized in production processes. Understanding this rate enables managers to optimize resource allocation and enhance overall operational efficiency.
Overall Equipment Effectiveness (OEE)
Overall Equipment Effectiveness (OEE) is a key metric that evaluates the efficiency of equipment in manufacturing operations. It considers factors like equipment downtime, speed loss, and quality defects to determine the overall productivity of machinery. This metric is beneficial as it identifies underperforming assets and areas for enhancement. By offering a detailed insight into production efficiency, OEE aids in streamlining processes and boosting output.
Utilization Rate
Utilization Rate plays a pivotal role in evaluating how effectively resources are being utilized within production facilities. By indicating the percentage of time resources are actively engaged in production activities, this metric highlights areas of inefficiency and excess capacity. It serves as a valuable tool for optimizing resource allocation, reducing wastage, and enhancing overall operational effectiveness.
Quality Indicators
Quality indicators such as First Pass Yield (FPY) and Defect Rate are crucial for ensuring product quality and customer satisfaction. FPY measures the percentage of products manufactured correctly without requiring rework, reflecting the effectiveness of production processes. On the other hand, Defect Rate indicates the frequency of defects in manufactured products, highlighting areas that require improvement to enhance quality standards.
First Pass Yield (FPY)
First Pass Yield (FPY) is a pivotal metric that signifies the efficiency of production processes in delivering defect-free products initially. Its emphasis on getting products right the first time enhances overall operational efficiency and reduces costs associated with rework. This metric is advantageous for identifying root causes of defects and implementing corrective actions promptly, thereby elevating product quality.
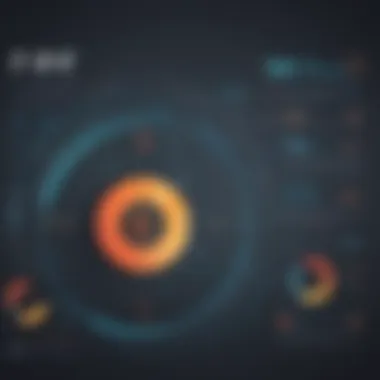
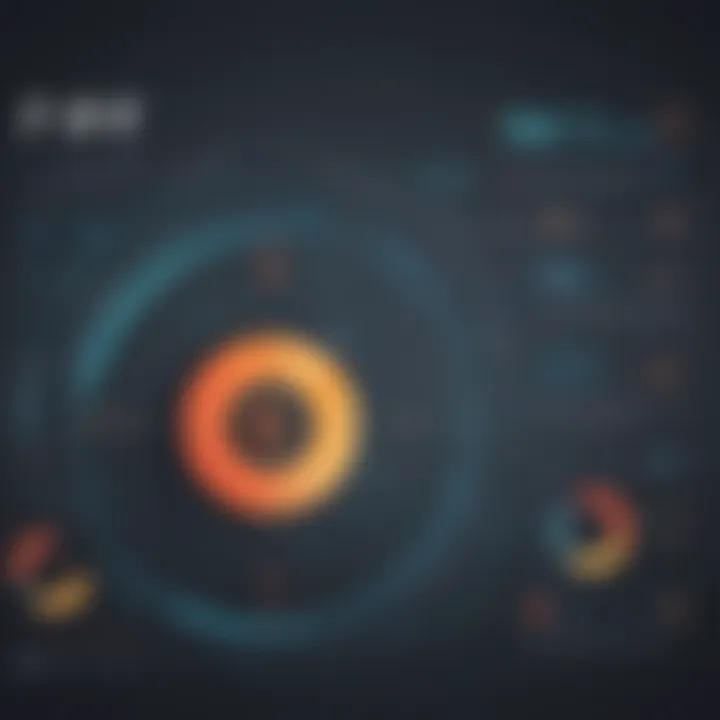
Defect Rate
Defect Rate serves as a critical indicator of product quality by quantifying the number of defects per unit produced. It aids in identifying trends in product defects, pinpointing areas for quality improvement, and guiding preventive measures to minimize defects. By focusing on reducing the Defect Rate, production managers can enhance product quality, customer satisfaction, and overall operational excellence.
Cost-Related KPIs
Cost-related KPIs such as Cost per Unit and Manufacturing Cost as a Percentage of Revenue play a pivotal role in assessing production costs and profitability. Cost per Unit calculates the average cost incurred in producing a single unit, providing insights into cost efficiency and profitability at a product level. Conversely, Manufacturing Cost as a Percentage of Revenue compares the total manufacturing expenses to the revenue generated, offering a comprehensive view of cost management effectiveness.
Cost per Unit
Cost per Unit elucidates the expenses associated with producing a single unit of a product, offering valuable insights into cost allocation and manufacturing efficiency. By tracking this metric, production managers can identify cost-saving opportunities, optimize production processes, and enhance profitability. Understanding the Cost per Unit is essential for making informed decisions related to pricing, resource utilization, and operational budgeting.
Manufacturing Cost as a Percentage of Revenue
Manufacturing Cost as a Percentage of Revenue provides a holistic view of cost efficiency by analyzing the proportion of manufacturing expenses relative to the total revenue generated. This metric helps in evaluating cost control measures, budget allocation, and overall financial performance. Maintaining a favorable ratio between manufacturing costs and revenue is essential for ensuring sustainable profitability and operational viability.
Safety and Compliance Measures
Safety and compliance measures like Lost Time Injury Frequency Rate (LTIFR) and Adherence to Regulatory Standards are indispensable for safeguarding employee well-being and ensuring adherence to legal requirements. LTIFR quantifies the frequency of workplace injuries resulting in lost workdays, emphasizing the importance of maintaining a safe working environment. Adherence to Regulatory Standards, on the other hand, ensures that production operations comply with industry regulations and standards, mitigating risks and enhancing organizational credibility.
Lost Time Injury Frequency Rate (LTIFR)
Lost Time Injury Frequency Rate (LTIFR) measures the frequency of workplace injuries that lead to employees being unable to work for a specific duration. This metric provides valuable insights into workplace safety, risk mitigation strategies, and the overall well-being of the workforce. Monitoring LTIFR enables production managers to implement proactive safety measures, reduce workplace hazards, and foster a culture of safety within the organization.
Adherence to Regulatory Standards
Adherence to Regulatory Standards is paramount for ensuring compliance with legal requirements and industry practices. By adhering to set standards and regulations, production facilities uphold operational integrity, build trust with stakeholders, and mitigate legal risks. Maintaining strict compliance not only protects the business from penalties but also reinforces a positive reputation in the industry, emphasizing commitment to quality, safety, and ethical practices.
Implementing KPIs Effectively
When it comes to optimizing production management, the section on Implementing KPIs Effectively plays a crucial role in ensuring the success of operations. By focusing on this aspect, production managers can align their strategies with organizational goals and establish measurable targets that drive performance improvements. Implementing KPIs effectively involves setting clear objectives that are directly tied to enhancing efficiency and productivity within the production environment. It enables managers to track progress accurately, make informed decisions, and identify areas for continuous improvement.
Setting Clear Objectives
- Aligning KPIs with Organizational Goals: The alignment of KPIs with organizational goals is a fundamental aspect of successful production management. By ensuring that key performance indicators directly reflect the strategic objectives of the company, production managers can measure performance in a way that drives overall success. This alignment helps in focusing efforts on areas that have the most significant impact on business outcomes, allowing for targeted improvements that contribute to sustainable growth. The unique feature of aligning KPIs with organizational goals lies in its ability to link day-to-day performance metrics with the broader vision of the organization, providing a clear roadmap for achieving success.
- Establishing Measurable Targets: The process of establishing measurable targets is essential for tracking progress effectively and assessing performance against set benchmarks. By setting clear and specific objectives that are quantifiable, production managers can measure success, identify areas needing attention, and celebrate achievements. This approach enables teams to stay motivated, understand expectations clearly, and work towards tangible outcomes. The advantage of establishing measurable targets lies in its ability to provide a concrete framework for assessing performance, facilitating accountability, and guiding decision-making processes throughout the production cycle.
Data Collection and Analysis
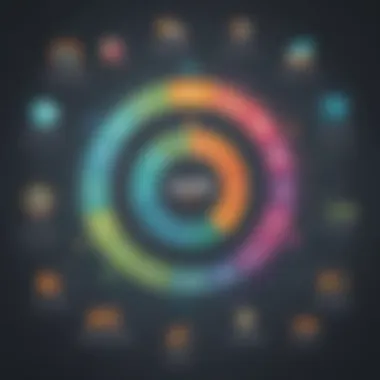
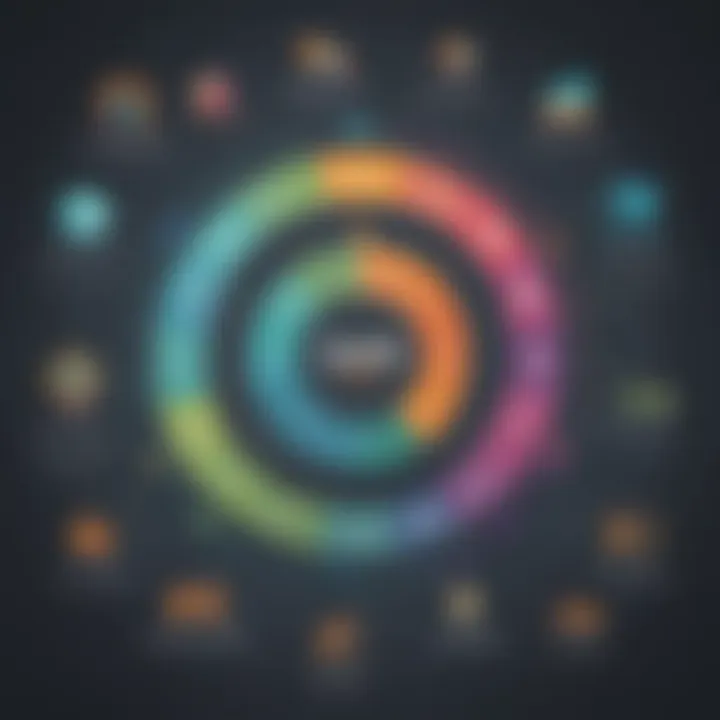
- Utilizing Technology for Data Tracking: Leveraging technology for data tracking enhances the accuracy and efficiency of performance measurement in production management. By utilizing advanced software and tools, production managers can collect real-time data, analyze trends, and gain actionable insights into operational processes. This technological approach streamlines data collection, reduces manual errors, and allows for informed decision-making based on reliable information. The advantage of utilizing technology for data tracking lies in its ability to automate processes, improve data accuracy, and enhance overall performance management within the production environment.
- Interpreting KPI Trends: Interpreting KPI trends is a critical aspect of data analysis that enables production managers to derive meaningful conclusions from performance metrics. By identifying patterns, anomalies, and correlations within KPI data, managers can make informed decisions, predict future trends, and proactively address potential issues. This analysis allows for the identification of opportunities for improvement, the optimization of resource allocation, and the strategic planning of production activities. The advantage of interpreting KPI trends lies in its ability to provide valuable insights, forecast performance outcomes, and drive continuous improvement initiatives within the production setting.
Continuous Improvement Strategies
- Kaizen Principles: Embracing Kaizen principles fosters a culture of continuous improvement and innovation within production management. By encouraging incremental changes, ongoing learning, and employee engagement, Kaizen principles drive operational excellence, enhance quality, and optimize processes for maximum efficiency. This approach empowers teams to seek perfection, eliminate waste, and pursue excellence in all aspects of production. The advantage of Kaizen principles lies in its focus on small, sustainable improvements that accumulate over time to deliver significant results, promoting a proactive and collaborative approach to performance enhancement.
- Lean Manufacturing Techniques: Implementing lean manufacturing techniques streamlines operations, eliminates inefficiencies, and reduces waste throughout the production process. By adopting lean principles such as value stream mapping, 5S methodology, and Kanban systems, production managers can enhance productivity, minimize costs, and improve overall workflow efficiency. This approach focuses on maximizing customer value while minimizing resources, driving a culture of continuous improvement and waste reduction. The advantage of lean manufacturing techniques lies in their ability to promote a culture of efficiency, flexibility, and continuous improvement, leading to sustainable growth and operational excellence in production management.
Monitoring Performance and Adjusting Strategies
In the realm of production management, Monitoring Performance and Adjusting Strategies stand as pivotal components in driving operational excellence. This segment delves into the critical aspects of overseeing performance metrics and making strategic adjustments to optimize production processes. By implementing a robust system for monitoring performance, production managers can effectively track key performance indicators (KPIs), identify areas for improvement, and ensure operational efficiency remains at its peak.
Regular Performance Reviews
Identifying Areas for Enhancement
Analyzing performance through regular reviews plays a vital role in identifying areas for enhancement within the production ecosystem. This structured evaluation process allows production managers to pinpoint inefficiencies, operational bottlenecks, and potential improvement opportunities. By focusing on enhancing identified areas, managers can gradually refine processes, boost productivity, and streamline operations for enhanced performance and profitability. The detailed scrutiny of metrics and operational data underlines the significance of this constant improvement approach in catapulting production management towards peak efficiency.
Addressing Bottlenecks
Addressing bottlenecks involves eradicating operational obstacles that hinder seamless production flow. By targeting these critical points of congestion, production managers can significantly enhance overall efficiency, reduce downtime, and eliminate potential disruptions. The proactive identification and resolution of bottlenecks contribute to a smoother production workflow, enhanced output capacity, and improved resource utilization. While addressing bottlenecks demands strategic planning and resource allocation, the results can lead to substantial performance enhancements and operational fluidity within the production environment.
Flexibility in Response
In the face of dynamic market conditions and evolving operational landscapes, flexibility in response emerges as a strategic imperative for production managers. Adapting strategies to changing conditions involves a proactive stance towards embracing shifts in demand, technology, or resource availability. This adaptive approach enables production managers to pivot swiftly, realign strategies, and optimize production processes in response to external dynamics. Embracing flexibility empowers production teams to stay agile, responsive, and resilient in the face of uncertainty while maintaining a competitive edge in the market.
Adapting Strategies to Changing Conditions
Tailoring strategies to align with evolving market dynamics is essential to sustaining operational relevance and competitive advantage. By recalibrating production strategies in response to market fluctuations, regulatory changes, or technological advancements, production managers can future-proof operations and seize emerging opportunities. This adaptive strategy ensures that production processes remain agile, efficient, and attuned to the ever-changing industry landscape.
Quick Decision-Making
The ability to make rapid, informed decisions is indispensable in today's fast-paced production environments. Quick decision-making empowers production managers to respond promptly to challenges, capitalize on opportunities, and address unexpected events effectively. This proactive decision-making paradigm enhances operational agility, minimizes delays, and fosters a culture of efficiency within the production setup. While quick decisions require a nuanced understanding of data, risks, and outcomes, they serve as catalysts for driving operational success and maintaining a competitive edge.
Collaboration and Communication
Efficient collaboration and seamless communication are fundamental enablers of success in production management. Cross-functional team meetings serve as forums for exchanging ideas, aligning strategies, and fostering cohesive teamwork across departments. These collaborative sessions promote knowledge sharing, problem-solving, and collective decision-making, enriching the production landscape with diverse perspectives and expertise. Embracing a culture of collaboration cultivates a unified approach to production challenges and fuels innovation and continuous improvement within the operational framework.
Cross-Functional Team Meetings
Engaging in cross-functional team meetings facilitates holistic insights, promotes interdisciplinary collaboration, and enhances synergy among diverse production stakeholders. These meetings serve as avenues for aligning objectives, resolving inter-departmental issues, and enhancing operational cohesiveness. By harmonizing perspectives and goals through cross-functional interactions, production teams can leverage collective expertise, optimize resource allocation, and drive unified efforts towards shared production objectives.
Sharing Insights and Best Practices
The dissemination of insights and best practices within production teams fosters a culture of learning, innovation, and continuous improvement. By sharing knowledge, successful strategies, and industry best practices, production managers can cultivate a knowledge-sharing ecosystem that encourages experimentation and refinement. This collaborative approach not only enhances operational efficiency but also nurtures a culture of innovation, adaptability, and excellence within the production domain. Leveraging shared insights enables teams to leverage experiential learning, embrace new methodologies, and drive sustainable growth and competitiveness in the production landscape.